Evkaz/iStock/Getty Images Plus
Deep hole drilling can range from the tiniest of diameters, like 0.015 in. found in microdrilling, all the way up to 20- to 30-in.-dia. holes found in shipyard and shaft work. Some deep hole drilling applications are so extreme that they are often unrealized by many in the industry. While present-day technology and equipment can handle the deepest and largest holes, not all applications require extreme depth-to-diameter ratios. Gun Drilling Machine For Sale
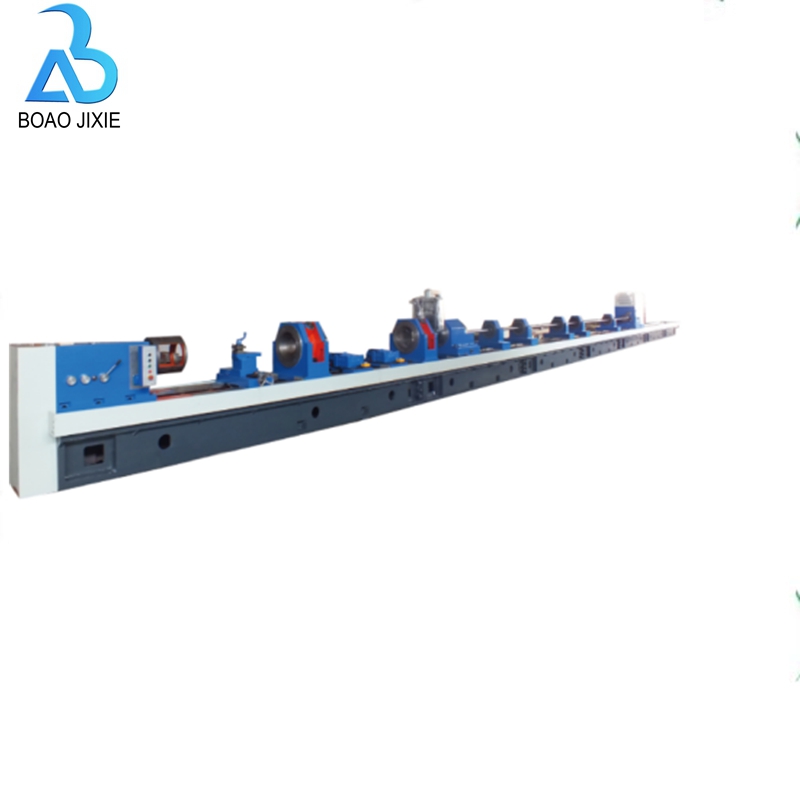
The diameter of the hole often dictates the type of technology needed and the depth-to-diameters that can be achieved.
Microdrilling is a unique process capable of producing holes in diameters from 0.0039 in. to a maximum of 0.059 in.
“In microdrilling, the machine, the toolholder, and the process, all will affect process capabilities and hole quality,” said Michael Herman, vice-president of sales, BIG DAISHOWA, Hoffman Estates, Ill. “As far as accuracy, machine runout or TIR [total indicator runout] in the spindle as well as toolholding is important to control. Coolant-through tools are an asset, if possible. However, when you get into anything beyond 30xD, coolant-through is not an option. Instead, using a nut that puts coolant around the face of the tool can help flush out the chips.”
First, you must ensure the machine is repeatable, particularly with tool changes. It’s important to verify the tool is repeatedly being put in the spindle accurately at the same location.
Second, a high-quality holder comes into play when accuracy is a factor. Whether you use a hydraulic or collet, make sure there is no runout. Doing so will help maintain tool accuracy and TIR and minimize breakage.
Third is process. For example, as drill depth increases towards that 80xD, it will not be a single-tool process.
“It may turn out to be a four-tool process to get you the tool life that you might need,” said Herman. “The process starts out with a spotting drill that actually produces a pilot hole and location. It is important that the pilot drill diameter is a couple microns larger (or have a plus/plus) tolerance than the actual hole diameter because you don't want to rub on the sides. It drills down to about 2xD.”
From there, the second tool could be a 9xD drill, depending on the material and how flat the entry is. And then it would increase to a 20xD drill and then 40xD drill to get to that 80xD.
“You could of course go back and drill all the way to that 80xD, but then you are putting all of the wear on an 80xD drill,” said Herman. “If we break up the process, it actually becomes more cost-effective to do it with multiple drills.”
SPHINX micro drills are designed to ensure maximum tool life, accuracy, and process reliability, even in the smallest diameters. They come with a wide range of unique drill point geometries, flute lengths, and shank diameters. BIG DAISHOWA
Another option is to start with a larger drill, like a 40xD drill, and create a pilot hole on a very low RPM. Once you drill the pilot hole (2xD), increase the RPM and turn on the coolant to start a pecking cycle to ensure that you are drilling down (2xD up to 5xD) and never coming completely out of the hole.
“Utilizing a variable-depth pecking cycle to control chip size, it will peck down and come out to the face of the part to flush chips. The drill doesn't exit because if the drill exits, it could whip and break when it goes back into the hole,” said Herman. “This can be very time-consuming, especially if you need to get from the pilot hole to an 80xD hole. There are a lot of pecks in there. The microdrill is solid carbide beyond the 10xD mark rather than fluted, meaning you have to come out of the hole more frequently to break up the chips.”
While microdrilling is fairly common, it does have a bit of a learning curve to ensure hole quality and straightness. If the hole is angled or out of tolerance, checking to ensure the machine is running properly is a good start. A change in material, such as going from barstock to a forging, or in material hardness can make a big difference.
“It’s important to adjust the pecking cycle as the drill depth changes,” said Herman. “Keep the more rigid tool, like a 20xD or 40xD over the 80xD, and only use it when needed to ensure both the drill stability and quality of the hole remains intact. You certainly don’t want to overfeed the drill.”
Microdrills have a unique carbide grain that provides more flexibility to the drill. Newer drill designs offer a degressive helix design to aid in hole location accuracy with a longer spiral flute to allow chips to be pulled out more effectively than a normal spiral flute drill.
Gundrilling tools are a go-to choice for machining centres as well as dedicated deep hole drilling machines.
“Gundrilling tools are designed for general, mainstream-diameter holes in the 1/8- to 1-in.-dia. range,” said Anthony Fettig, CEO, Unisig, Menomonee Falls, Wis. “They can go larger, but there is an economic point where it starts making less sense.”
Gundrilling produces 20xD to 30xD holes with ease as long as the machine has high-pressure coolant-through the spindle and chip control is managed through the cutting parameters.
“Generally, you can drill a 20xD or 30xD hole with a gundrill without much trouble,” said Fettig. “However, when you get to 40xD, it becomes more challenging because, at this point, the tool will start to whip and you really notice the physics of deep hole drilling come into play.”
Drift management starts to become a big part of the discussion as you move towards 100xD. In these cases, it’s important to understand the nature of the hole. Does there just need to be a hole? Or does it need to be a straight hole in a specific tolerance?
A BTA drilling system can typically produce hole sizes anywhere from 5/8 in. to as large as the machine can handle. BTA really shines in deeper holemaking applications, like the 100xD, where it produces better-quality holes and uses a much higher feed rate than its gundrilling counterpart. Sunnen
There is a strategy in cutting high depth-to-diameter holes. One way to offset hole drift is counter-rotation of the part, which can be done very effectively with cylindrical parts. If counter-rotation is not an option, revert to metal cutting best practices, according to Fettig.
“Sometimes you may need to reduce the cutting forces and reduce the volume of chips needing to be cleared,” said Fettig. “You might start with a higher feed on the first half of the hole, then slow down the deeper you get to manage the forces. This works a lot better if you start with a short drill. Drill half the hole with a short drill and then use a longer drill to finish it.”
In applications where holes are on the extreme end, around 400xD range, the tool might need to be changed out six or more times to reach the depths effectively.
“A good rule of thumb is to use the shortest tool possible to drill the hole. For a 100xD hole, it’s not advisable to put a long, skinny, non-rigid tool in the machine and hope for the best,” said Fettig. “This is especially true for machining centres where they don’t have whip guides to keep the tool straight. Following an effective drilling strategy will ensure a good-quality hole.”
A deep hole drilling machine will have guided systems outside the hole to stabilize the tool as it’s drilling. This enables you to produce a 100xD hole from start to finish using one tool. However, be sure to reduce the feed more than you would if you sequenced the hole with multiple tools.
“With the BTA drilling system, typically hole sizes will start anywhere from 5/8 in. and then can go up as large as the machine can handle,” said Mark Sollich, business development manager, Sunnen, St. Louis. “However, as the tool gets bigger, more horsepower is needed to drive the tool and more coolant pressure is needed to clear the chips. Today’s machines can often cover a variety of different sizes.”
If the hole is under 1 in., both a gundrill and a BTA drill are suitable options. However, it’s important to note that with deep holes in the 100xD range, BTA often will produce a better-quality hole and use a much higher feed rate than its gundrilling counterpart.
Once you get into 2-in.-dia. holes, BTA drilling is almost always the right choice because it provides better proportional rigidity than gundrilling so the holes tend to be straighter.
“With BTA at the 100xD range, you don’t have to slow down in order to maintain straightness,” said Sollich. “If the part is solid, like a billet, you will have to create an initial hole using something like a drill with indexable inserts and indexable guide pads.”
In situations where the application requires very tight tolerances and a very straight hole with good surface finish, it may not be enough to just drill the hole.
Bottle boring can be performed to contour the inside of the bore. For example, once a pilot hole is created, it can be fixtured and programmable contour turning can be applied to create a feature for a landing gear component or a part for the oil and gas sector. Unisig
“The drilled hole may require a counterboring tool to open that hole up to a larger size,” said Sollich. “Counterboring will help reduce the amount of drift in the hole by about half. The most accurate of these tools is a pull counterboring tool. Instead of pushing the tool like a drill, you introduce the bar through the inner diameter (ID) of the part that already has a hole in it. You screw on the pull counterbore tool and pull it through the existing hole.”
This tool creates an extremely straight hole with high accuracy because of the constant force and tension on the bar as it’s pulled through.
“After counterboring, you can go into the hole with a skive and roller burnishing tool,” said Sollich. “This will open up the hole even larger. The skiving tool will create uniform peaks and valleys in the bore. On the backside of the tool, it has a row of burnishing tools, which mashes down the peaks and valleys in the bore, cold works the material, opens up the hole, and produces a very smooth surface finish, anywhere from a 4 to 6 Ra surface finish, almost like a mirror.”
Successive counterboring also is a common practice. For example, if the hole is drilled to a 3 in. dia. down 20 ft. deep., use a counterboring tool to open the hole to 3.25 in. Make another counterboring pass to widen it to 3.5 in., and repeat until the hole is at its intended diameter.
“We can then put in a radius transition between the big and small hole, meaning that the hole gets three times the successive finishing, tolerance, or dimensional targets,” said Fettig.
Bottle boring can be performed to contour the inside of the bore. For example, once you’ve created the pilot hole, fixture it and apply programmable contour turning to create a feature for a landing gear component or a part for the oil and gas sector.
“While drilling a hole is important, it’s not all that can be done,” said Fettig. “It’s all about creating a complex, deep hole machined to a feature.”
However, when you get into very large diameters, trepanning is a process that should be considered. This process will create a solid slug from the interior of the hole diameter.
“For example, when you trepan a 10-in.-dia. hole, the hole itself is exactly the correct size, but you then also get an 8- or 9-in.-dia. core of material that comes out,” said Sollich. “This material can be used for smaller components or sold to other shops. Not only are you reducing material costs but on overage, this process requires 30 per cent less horsepower than a drill. That’s another benefit.”
A blind hole may often need to be finished to include a flat bottom, which includes additional operations.
“After drilling, the next operation would be a form tool,” said Sollich. “You would screw the form tool on the same bar, feed the tool down to the bottom of the hole, and feed it to whatever the bottom configuration is. For a flat bottom, a form cutter or blade on the roll will create the configuration at the bottom of the hole.”
And while a flat-bottom hole may be more commonly found in large-diameter holes, they are less common in microdrilling, especially when you get into the very large depths.
“A flat-bottom hole is a challenging operation at 80xD in microdrilling,” said Herman. “It’s typically a hole with a drill depth or drill through.”
Associate Editor Lindsay Luminoso can be reached at lluminoso@fmamfg.org.
BIG DAISHOWA, www.bigdaishowa.com
Canadian Metalworking / Canadian Fabricating & Welding
Toronto, M1R 0A1 Canada
See More by Lindsay Luminoso
Lindsay Luminoso, associate editor, contributes to both Canadian Metalworking and Canadian Fabricating & Welding. She worked as an associate editor/web editor, at Canadian Metalworking from 2014-2016 and was most recently an associate editor at Design Engineering.
Luminoso has a bachelor of arts from Carleton University, a bachelor of education from Ottawa University, and a graduate certificate in book, magazine, and digital publishing from Centennial College.
Read more from this issue
Find Canadian Metalworking on Facebook
Find Canadian Metalworking on Twitter
Keep up to date with the latest news, events, and technology for all things metal from our pair of monthly magazines written specifically for Canadian manufacturers!
Easily access valuable industry resources now with full access to the digital edition of Canadian Metalworking.
Easily access valuable industry resources now with full access to the digital edition of Canadian Fabricating & Welding.
Check out the Milltronics VM4222IL with rotary/tilt table. The VM4222IL features travels of 42 x 22 x 24 in. and a 46 x 22 in. table as well as a 24 HP dual wound 10,000 RPM BIG-PLUS® spindle. Visit Milltronics.com to learn more.
© 2024 FMA Communications Canada, Inc. All rights reserved.
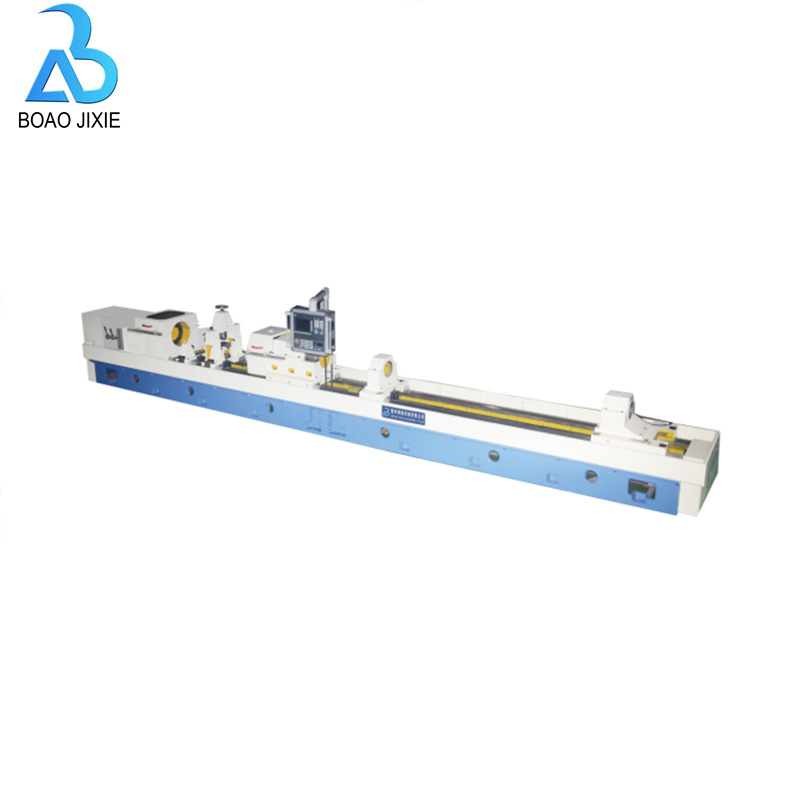
Iscar Deep Hole Drilling Not yet registered? Sign up