India’s positioning as the world’s textile recycling hub rests heavily upon the small town of Panipat, an approximate two-hour drive from country’s capital city of New Delhi.
Many of the textile recycling units in Panipat are small and medium enterprises, engaged in this process for more than 50 years, and now moving on to the second and third generation of factory owners. A variety of recycling takes place—with textile waste, both domestic pre-consumer and post-consumer, as well as imported. wrap dress
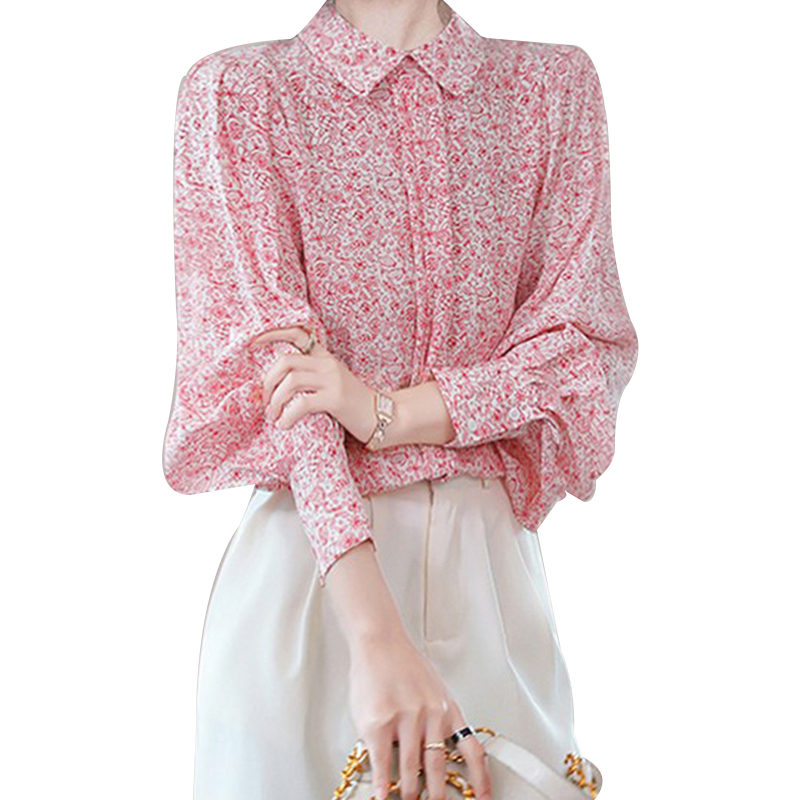
A.L.C. Teams with SuperCircle, Archive on Resale and Recycling
Better Cotton Points to India as Example of Pesticide Progress
Marquee Links With Apparel Group to Bring 5 Brands to New Markets
Pre-consumer textile waste consists mostly of post-industrial waste from textile factories, while post-consumer comes from used garments and household textiles, etc. Imported textile waste makes its way to Panipat from the Indian port city of Kandla.
The global push toward circularity, and the need for adaptation and change, has been permeating the city and bringing in a sense of unity with other manufacturers and stakeholders across India.
Of late, upgrading technology has been a focus.
“A lot of capacity building has been happening in terms of recycling, at least five to six times growth in the last 10 years,” said Gagan Kansal, director, Kay Gee Enterprises. “In the last 10 years garment production has increased substantially all over the world, and recycling has naturally stepped up as well. We have doubled in size in last few years and now do 20 tons a day, which is approximately 50,000 to 60,000 garments every day. An approximate 10 tons of this is post-consumer, or end-of-use garments.”
“It doesn’t hinge only on the European Union changing focus, nor on new brand sustainability orders—although those are fostering change, too. Mostly, entrepreneurs in Panipat are self-evolving. The new generations are also bringing in change,” he added.
In this case, his son Archish Kansal, who is also a co-director at the company, is taking the concept further, meshing technology with an understanding of the process and the market.
Representing the changing business approach, Archish Kansal is quick to point out that the Indian recycling industry “has never received its due for the kind of work we have been able to establish here,” but that the long-deserved recognition for the industry had started coming in with the growing focus on sustainability and circularity. “We are trying to see how we can internationalize more, bring in more stakeholders, talk to governments, talk about the policies and legislation needed,” Archish Kansal explained.
“Panipat has always been a textile and recycling hub, but now a lot of machinery has been added in a lot of factories. Many of the companies here are small and medium enterprises and don’t have the funds to make a bigger set up. That also becomes a strength in one way, because recycling needs a lot of careful monitoring and attention which is easier in a smaller company.”
Meanwhile, the local knowledge, forged over decades, remains as well. For example, sorting and separation continues to be done manually at most of the factories in Panipat. “The people who are sorters in Panipat can just touch the material and tell whether it is cotton or polyester, it is the traditional skill they have learned from their ancestors,” Archish Kansal said.
Panipat, however, is not the only textile recycling cluster in India.
Tirupur, in Southern India, and a hub of knitwear production, has been growing into an efficient and modern cluster for recycling, with a focus on pre-consumer waste. Amroha, a city in the state of Uttar Pradesh, is largely working with the downcycling of textiles, where discarded inputs are recycled and repurposed into something of lower value.
While each of these areas have different focuses, each is seeing growth. Entrepreneurs in the different regions agree that the recycling sector has barely touched the tip of the iceberg. If the largely informal sector is able to come together to create synergies and efficiencies of scale, India’s potential for both global and domestic recycling is huge.
India’s potential in this space is best encapsulated in a first-of-its-kind study by Fashion for Good, the platform for sustainable fashion innovation, released in July 2022.
The report, “Wealth in Waste: India’s potential to bring textile waste back into the supply chain” shared insights, numbers, and ways to better grow, citing that of the 7,793 kilotons of textile waste handles annually in India, an estimated 51 percent is post-consumer waste, originating from local consumers. Another 42 percent is pre-consumer wastes. Seven percent is imported waste.
Produced by a joint team from Fashion for Good, Sattva Consulting, Reverse Resources and Saahas Zero Waste, the report noted that India’s “decades-old embedded culture and history of reusing, remaking and redesigning garments has enabled informal trade routes for textile waste and infrastructure to flourish.”
Stakeholders involved in the creation of the report told Sourcing Journal that India stood at the cusp of a huge opportunity to emerge in a leading circular sourcing position.
“Over the years, despite the absence of technology, the Indian textile recycling ecosystem has established a strong hold in mechanical recycling by way of manual sorting, combining specific colors and fibers to reach desired quality. By doing so, they have been able to extract economic value even from nonrecyclable waste. However, this infrastructure and expertise has been handled by informal channels. Value chains can be formalized to establish circularity of textile waste in India if this infrastructure and technical know-how is supported by brands, governments and investors,” the study noted.
It also highlighted relevant details: most notably that more than 60 percent of waste is made of cotton and cotton rich materials.
As for an overall breakdown of India’s total textile waste of 7,793 KTons—3,265 KTons are pre-consumer waste; 3,944 KTons are post-consumer domestic waste and 584 KTons are imported waste.
Anjali Krishnan, program manager, IDH, a Netherland-based organization which works in countries around the world to catalyze positive change for the environment and gender equality, has been actively connecting the dots.
“There is a lot to be done,” she said. “We have to find more solutions. How do we aggregate the textile waste, segregate it and ensure it reaches the correct recycler or manufacturer or brands so that it comes back into production? These are some of the big challenges.”
“A lot of our focus is to use the post-industrial waste more efficiently, so that the correct quantity of waste reaches the right locations. There are capacity training issues as well—If the value chain is not properly activated, a lot of good waste won’t reach the correct source. For example, it may be downcycled instead of getting recycled, because either they didn’t get the right quantity, or they did not have the knowledge,” she said.
She said an ideal scenario would be a closed loop. “For example, if a company like H&M were to generate post industrial waste and it comes back into their system. But right now, a company will buy waste—not just theirs—but post industrial waste from others as well,” Krishnan explained, citing the growing need for traceability.
“Everyone is seeing the potential of textile waste,” Krishnan observed. “But down the line India may not be the largest importer of textile waste, as the European Union policies don’t allow much of export. Bangladesh has been a major exporter of textile waste, but as they are trying to grow in this space, that may stop. India has an established system, we are pushing innovation, but how are we going to get the raw material?” she queried.
It is clearly time for better road maps and the report from Fashion for Good has ignited more conversations around that idea.
“The industry stands to gain with a clear map of the textile waste value chain in India, armed with a robust set of recommendations for action. This now forms a strong basis to move forward collaboratively to scale the investments, infrastructure and innovation needed to make circularity in fashion a reality in India,” Anita Chester, managing director, Laudes India LLP noted in the report.
Meanwhile, the competition continues to grow, not only between countries, but within the recycling units themselves. It is not all adversarial, however.
“We are learning from each other,” Archish Kansal pointed out gamely. “The best learning comes from the competition.”
This article ran in the Sustainability Report: Measuring Impact. To download the full report, click here.
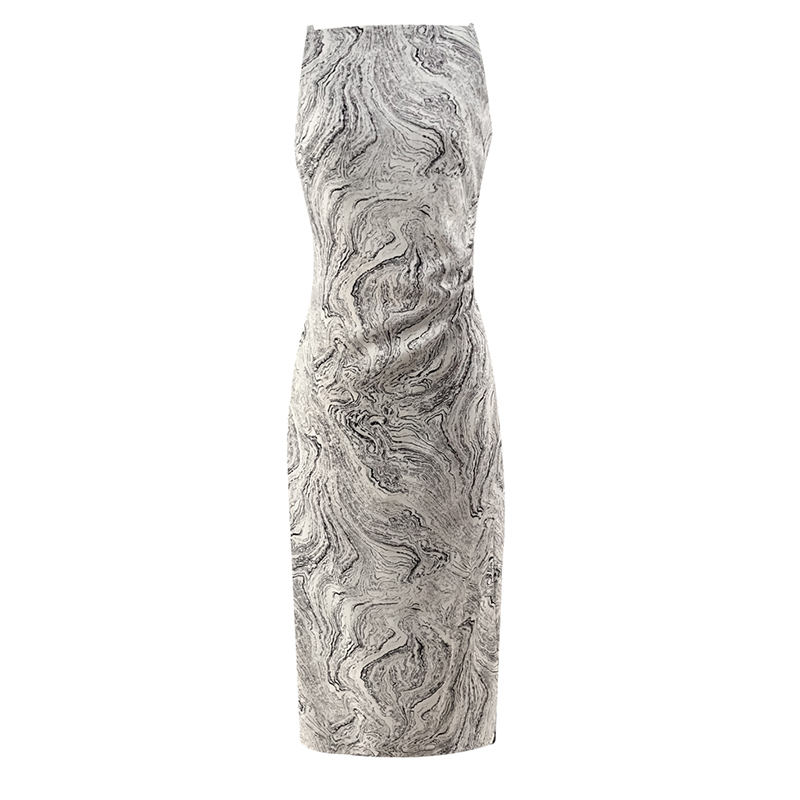
H&M Dresses Click here to read the full article.