A degree of confidence is essential when researching which valve type and material to use in an application. Besides understanding the function of valves, selecting the right material is one of the most critical decisions. Combining the appropriate valve type equipped with body material and elastomeric material that are compatible with the process is key to satisfying any application.
Chemical resistance is defined as the ability of a given material to withstand a chemical attack for a specified period. In valve selection, thermoplastic and elastomeric materials are typically chosen that best satisfy the application, based on lab-performed tests and real-world application testing. When any given material is designated as incompatible for an application, it either did not satisfy the application/performance testing in the lab or a failure occurred while the product was in service. When field failures occur, manufacturers’ material science engineers will try to duplicate a user’s experience in a lab environment. However, it can be challenging to recreate field failures in a laboratory environment. These challenges are typically related to unknown circumstances in the field application, such as pressure or temperature spikes, varied concentration of supplied chemicals or other human factors. Cr Neoprene
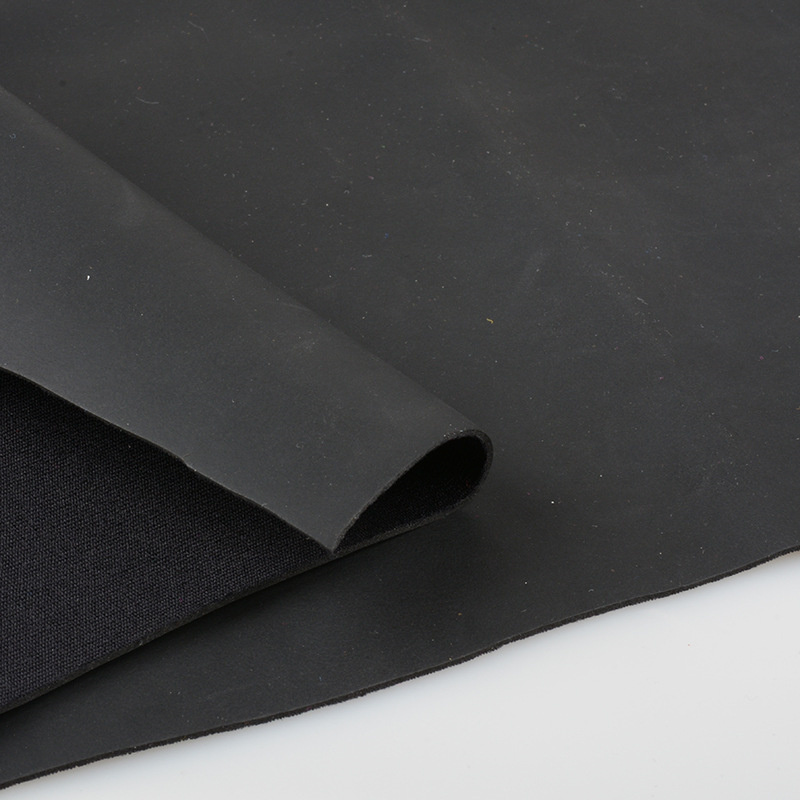
Chemical compatibility ratings can typically be found on online resources from manufacturers. Manufacturers may advise against using general guidance from other resources to select their product. It is always beneficial to consult the manufacturer prior to use of their product in a given application.
Chlorinated polyvinyl chloride (CPVC) type valves and piping resins have different chemical compatibility. Sodium or potassium hydroxide, commonly known as caustic solutions, are chemicals typically used with CPVC piping and valves. However, different CPVC resin manufacturers may have different chemical compatibility results, which reinforces the idea to always check with the manufacturer prior to specification or installation.
For elastomers, fluorocarbon rubber (FKM) seals will fail in caustic applications. Because of the risk of FKM failure, ethylene propylene diene terpolymer (EPDM) is typically supported for these applications with long-term success. EPDM has proven, through application testing in swimming pools, to be moderately resistant to the effects of chlorinated water. In those situations, using high-quality EPDM with a low amount of vulcanizing agents and fillers can be supported.
The first point of attack will be the liner on a butterfly valve, but well-controlled water chemistry (i.e., chlorine that has fully dissolved in water) along with moderate temperature control will maintain an even concentration of chlorine in the water to lessen any effect. However, EPDM is not recommended for chlorine gas or chlorine dioxide introduction commonly used for water treatment. EPDM has proven to be an effective elastomeric choice only in a closely controlled aqueous solution, like swimming pools.
Specialty fluorinated elastomers provide extreme chemical resistance due to their strong fluorine bonds. They combine with the thermal resistance of FKM rubber to provide resistance to chemicals and environments where typical FKM elastomer may fail. These specialty elastomers will come at an increased cost compared to standard FKM. Perfluoroelastomer (FFKM), FKM extreme and FKM ethylene, tetrafluoroethylene and perfluoromethylvinylether (ETP) allow for better resistance due to ethylene, tetrafluoroethylene and perfluoromethylvinylether properties.
Additionally, they may perform better at low temperatures than conventional FKM. These are potential options for ball valve O-rings, which become saturated in the media fluid. Contact the valve provider and ask for the O-ring sizes the valve requires when using any specialty elastomer. Only replace valve O-rings with the proper size(s) that are specified by the manufacturer and follow all manufacturer assembly and testing procedures prior to valve installation.
Sodium hypochlorite service is a widespread application primarily used to disinfect water during municipal water treatment. An engineer-preferred valve for dosing of sodium hypochlorite is the diaphragm valve. This type of valve provides good overall control through a non-rising multiturn handwheel, which activates the linear travel diaphragm to either open or close the valve. Most diaphragm valves feature a raised center section, known as the weir. For chemical feed applications, controlling the opening between the raised center section and diaphragm is key to control. Molded flanged vinyl valves do not utilize solvent cement to connect a separate flange to the valve spigot. This exclusion eliminates cemented joints that come under attack from sodium hypochlorite. The molded flanged diaphragm valve can also be utilized with other piping materials since it can be connected without solvent cement.
The next and most popular solution is a ball valve with molded flanged end connections; however, true-union valves with socket ends are another option, which tend to be preferred in the industry. O-rings should be made from FKM for ball valves in sodium hypochlorite applications. A 1/8-inch vent hole in the ball cavity is an additional added feature to prevent sodium hypochlorite and other off-gassing media. This inclusion eliminates pressurization in the cavity of the ball valve when the valve is closed. The question then becomes whether to vent to the upstream side of the piping system or downstream.
While either solution will eliminate the pressurization by permitting the off gassing to escape the cavity of the ball, extensive testing helps to determine the nuances between the two methods. When venting the ball on the upstream side of the valve, the fluid captured in the cavity of the ball when the valve is closed is maintained by the positive upstream pressure. As a result, the cavity remains fluidized. Venting downstream causes the trapped product to crystalize as the upstream fluid does not maintain it.
When selecting a valve for any chemical application, there is usually more than one possible solution. During the valve selection process, it is imperative to give careful consideration to a material’s chemical resistance in order to provide the end user with a robust solution that is ensured to perform at a high level. It is always advised to consult your manufacturer when in doubt to remove the risk of improper material selection. Manufacturers will be able to provide material compatibility recommendations and suggestions on location, layout and other environmental considerations, which will enhance the performance of the pipeline.

Waterproof Sbr Dave Hurley is a product information manager at Asahi/America, Inc. located at the company’s Lawrence, Mass. headquarters. He may be reached at dhurley@asahi-america.com or 781-388-4576. For more information, visit asahi-america.com.