Engineers around the world are designing increasingly compact products. To meet their needs, igus®, the Germany-based manufacturer of motion plastics, has developed micro gears with modules down to 0.2. The gear teeth have dimensions very close to that of human hair. However, thanks to high-performance plastics, they still allow low-wear, precise movements for high-quality products despite the minute size.
As a photographer zooms in with their camera, a gear system composed of extremely small gears moves within the lens—just a few millimeters in size. The teeth on these gears are even smaller, barely discernible to the naked eye. Motorized Ball Valve Actuator
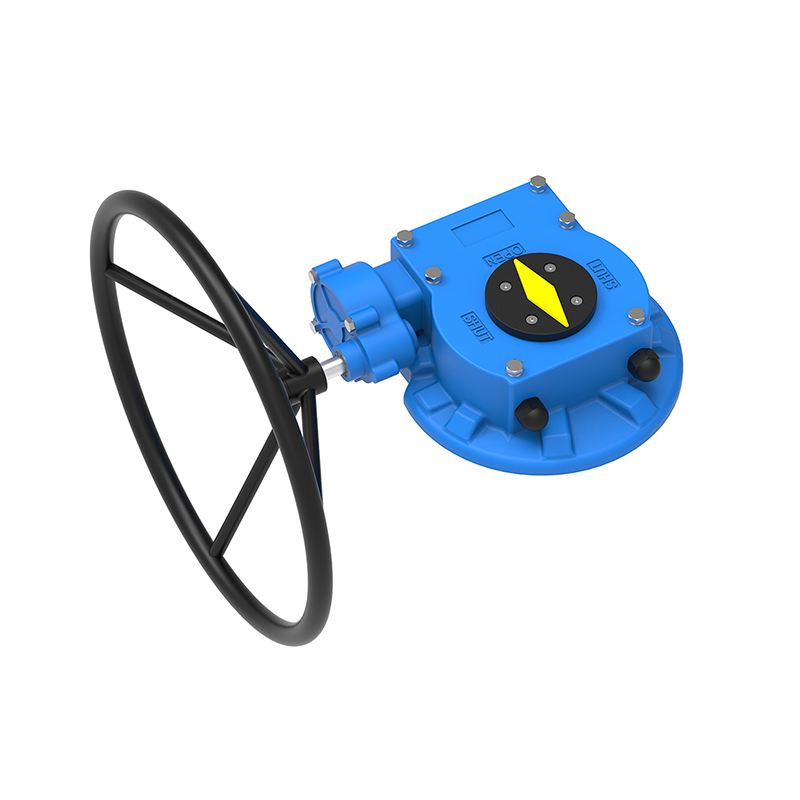
“For such precision mechanics applications, designers need micro gears that are nevertheless stable and low-wear enough to operate reliably for years,” explains Steffen Schack, Head of the iglide Gears division at igus. “We have therefore optimized our manufacturing process to mechanically manufacture micro gears with modules down to 0.2 using high-performance plastics.” The company utilizes iglide® semi-finished products, including iglide A180 and iglide A500. The materials are tribologically optimized, meaning they have excellent properties in terms of friction and wear coupled with robustness. At the same time, they are significantly lighter than metal gears.
With modules down to 0.2, the polymer specialist has pushed the limits of its mechanical manufacturing even further. “Producing gear teeth that are barely discernible to the naked eye is an ability that sets us apart from many competitors in the market,” emphasizes Steffen Schack. “Despite the minute size, the teeth exhibit excellent mechanical properties. They enable highly precise, reliable movements in precision mechanics.”
igus now offers customized manufacturing of micro gears made of high-performance plastics.
“Our mechanical manufacturing from iglide semi-finished products also allows cost-effective pricing even for small batch sizes. For larger batch sizes, for example, for automobile mass production, we can manufacture by injection molding,” explains Schack. Schack also noted that the gears are suitable for numerous applications requiring finely tuned movements in confined spaces – such as for microscopes and other optical instruments, as well as miniature motors and microdrives.
Browse the most current issue of Design World and back issues in an easy to use high quality format. Clip, share and download with the leading design engineering magazine today.
Top global problem solving EE forum covering Microcontrollers, DSP, Networking, Analog and Digital Design, RF, Power Electronics, PCB Routing and much more
The Engineering Exchange is a global educational networking community for engineers. Connect, share, and learn today »
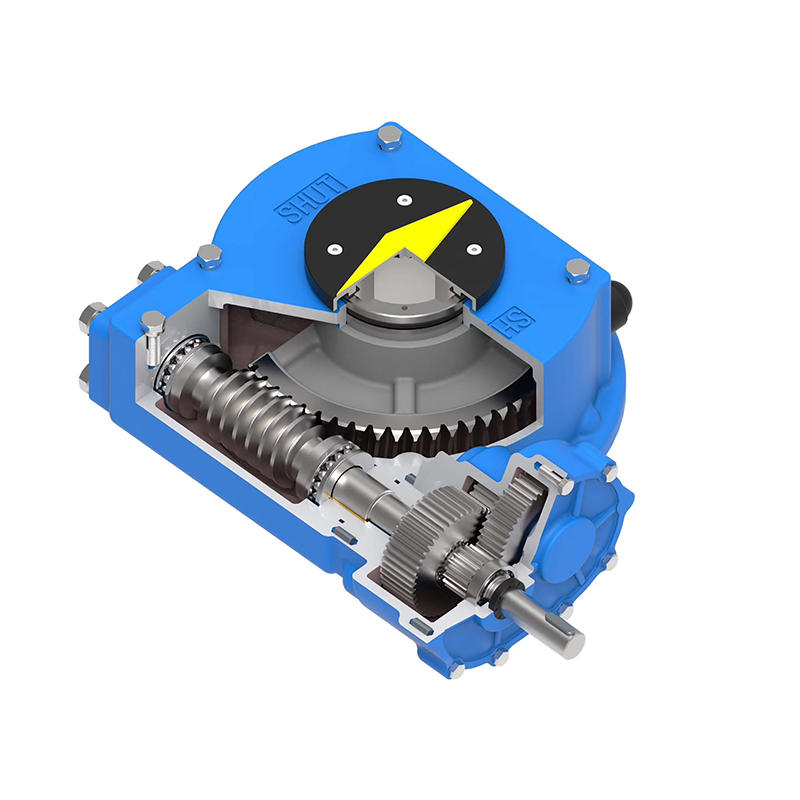
Manuel Gearbox Copyright © 2024 WTWH Media LLC. All Rights Reserved. The material on this site may not be reproduced, distributed, transmitted, cached or otherwise used, except with the prior written permission of WTWH Media Privacy Policy | Advertising | About Us