Ah, soldering. It’s great for sticking surface mount parts to a PCB, and it’s really great for holding component legs in a plated through-hole. It also does a pretty great job of holding two spliced wires together.
With that said, it can be a bit of a fussy process. There are all manner of YouTube videos and image tutorials on the “properest” way to achieve this job. Maybe it’s the classic Lineman’s Splice, maybe it’s some NASA-approved method, or maybe it’s one of those ridiculous ones where you braid all the copper strands together, solder it all up, and then realize you’ve forgotten to put the heat shrink on first. Fine Magnet Wire
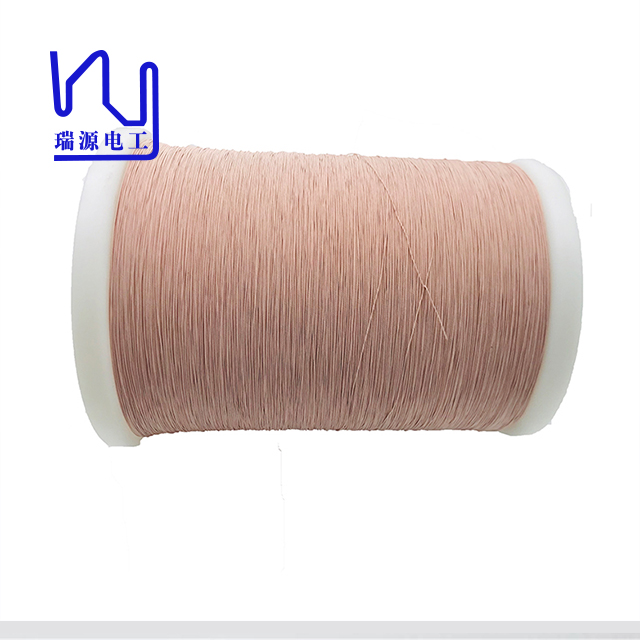
Sure, soldering’s all well and good. But what about some of the other ways to join a pair of wires?
These days, there are all kinds of ways to join a pair of wires. Some are relatively new-fangled and nifty, while others have been around since nearly the dawn of all this electrickery business. Let’s list off a few, and you can tell us your favorites and all the ones we missed in the comments.
First up is the solder-seal connector. Yes, you got us, this is still essentially soldering, but it’s kind of streamlined compared to doing it all by hand. We’re not entirely sure when the solder seal connector was invented, but it was probably in the 1980s, given the 1988 date on this US patent for the invention. Solder seal connectors are basically a piece of heat shrink tube with a blob of solder in the middle, and two blobs of heat-activated adhesive on either side. To use one, you take two wires, and then mesh the stripped ends together ready to be soldered. Then, you slide the solder seal connector over the join such that the solder bead is over stripped wire to be soldered. Heating the solder seal connector with the heat gun will melt the solder creating an electrical joint, while also shrinking the heat shrink and activating the adhesive to grab on to the insulation of each wire. You end up with a tough, waterproof joint in pretty much two easy steps. Plus it’s usually less blobby than your own efforts to solder a splice by hand.
Of course, then we have crimps. Crimps are great, if you use proper crimp tools and the right crimps that go with them. They’re a great way to make connections quickly and cleanly with zero heat. They’re credited in some contexts with being more reliable than solder joints, too, particularly in applications like aerospace or motorsport. Of course, if you use crappy crimp tools or crimps or just mismatch them, you’re in for a lot of pain. You’ll get pullouts and failures and all kinds of issues. They can also be expensive if you’re using super fancy crimps with certain connector families, but for joining two wires together, they’re usually pretty cheap.
For those uninterested in learning to operate a soldering iron or a crimp tool, there are even simpler solutions. 3M ScotchLoks, in their most primitive foldable form known as the 560, are considered a great way to join wires if you want to do a terrible car stereo install on the cheap. Go on, buy a $2000 beater off Craigslist or Facebook Marketplace, pull out the stereo, and you’re sure to find a nest of these awful plastic monstrosities. You thread two wires through, and then force the clasp closed, which forces a metal blade to slice through the insulation and grip both wires.
In practice, unless you have your wire types and gauges perfect, they often tend to cut or damage the wire and eventually fail. Worse if there’s movement that allows them to flex and chew their way through a wire. They also hurt your hands to use and offer no protection against the elements. Better solutions do exist in this category. More advanced ScotchLok and PressLok products exist, often with gel fillings that offer corrosion resistance and more reliable gripping of the wire without damage.
More recently, though, Wago connectors have grown in popularity. They’re a sort of deluxe-looking lever-close terminal block solution. When the lever is lifted, an internal metal contact is lifted. When the lever is placed back down, it grips the wire. By using a seperate lever and contact for each wire to be joined, the Wago connector can be used to join different wire types and gauges quite easily.
They’re becoming popular for use in all kinds of contexts, from DIY electrical work to more serious industrial uses.
We’ve listed a few of the most popular solder-ish and non-soldery ways to join wires and make electrical connections, now it’s over to you. What works, and what doesn’t? What did we miss? Sound off below and tell us your ultimate solutions for these jobs, especially when soldering isn’t the go-to.
Featured image: “Streamlining multiple wires” by [gratuit].
Wagos cost a small fortune, but they *just might* be worth it. It’s also nice that you can connect solid wire core to braided wire easily with them. Personally I like the 1 slot extenders that you can use to increase a wire run. I tend to plan poorly, and use them a lot.
You should get a wago kit, I think I paid 100usd for a kit at an electricians store with 400 wagos in 2,3,5x20A and 3x32A a few years ago.
BigClive covered Wago clones, and some seem better than the OG thing: Inside a Wago connector and a clone – https://www.youtube.com/watch?v=jQ4tB5_GH7w Clone of Wago product that Wago don’t even sell??? – https://www.youtube.com/watch?v=OP86SxqP7I8
I’d still be careful with clones. There are also suppose to be waterproof Wagos.
The Wagos are also nice for splices. I just used their 3-in 6-out units to splice WS2812B led wires.
Wago is nice because the wires all move together instead of getting pulled apart like a ScotchLok, but boy do they look ugly and make a tangled rats nest of wires. They are pretty reasonable for power on a car where there is a common ground so you only one of these Wagos in an area.
I only use crimp because it’s cheap in the long term, once you have a decent crimp tool. Cutting off the crimps to rewire something is financially less painful than the fancier connectors. The trick to all of these things is be prepared to screw it up the first few times and just redo it until you get it right.
In Germany Wago is all that is used by electricians. But as they usually work with 1.5mm² to 2.5mm² solid copper wire (at least when wiring houses), they use the much! smaller and cheaper Wago 2273 series.
Solid wires can not be pulled from those unless you twist them a few degrees back and forth while pulling them. If you have done that a few times re-wiring is a breeze with those connectors.
Clamped Wagos like the shown above are solely used if you need to connect litz wire to solid copper wire. Examples are thermostats, light fixtures, …
The clamped Wago is the middle ground between screw terminals/solder and alligator clamps on my workbench. Usage mainly depending on the prognosed frequency of dis- and reconnects in the near future.
Proper litz wire is not just stranded wire — every strand of litz (Litzendraht) wire is individually insulated to get lots of surface for skin effect and so that sort of connector would do a terrible job.
Do you have any data to support this claim? I’d have understood that the difference in metal type could cause a loss here.
To compare, take a usual screw: you’re connecting a solid 2.5mm2 copper wire, the outside perimeter is 5mm long. On this circle, you’re typically screwing a M3 screw tip flat on one side, so the actual contact area is ~7mm2. That’s 7mm2/5mm*3mm = 46% of the surface in contact. 15mm2 is the surface of the complete wire cylinder under the screw.
For a wago connector, you have a flat blade that’s bent on the wire, and it’s is 2mm to 3mm long on half the surface of the wire (so the contact area is 3mm*2.5mm = 7.5mm2 or 50% of the total surface of the wire).
We are largely over the required margin for transmitting an current of 20A on copper with such surface area, so it’s safe for both connectors.
Wikipedia isn’t a source but look at an illustration of what they’re saying https://en.wikipedia.org/wiki/Litz_wire#/media/File:Lica.png
You’ll need to remove the insulation first if you find wire like this.
I’ve used Litz wire from teeny tiny IF transformer size to about #6, welding size (used in a 1200 amp peak current inverter power supply). Yes, they are all insulated strands. Magnet wire insulation needs to be chemically stripped with acid, other kinds are thermally stripped which is much easier.
Yep, Litz have to be insulated otherwise it’s not Litz, it’s just fine stranded cable… if they would be not insulated then you wouldn’t get the nice skin effect reduction you seek when using Litz…
Litz wire != stranded wire. I think you meant stranded? Litz wire is finely stranded wire that’s insulated at the strand level (like a bundle of magnet wire) and used in high frequency applications (think Mhz)
Yep, I meant stranded wire. Here stranded cable is called Litze, so I confused those as English isn’t my first language. Sorry for the confusion!
“but boy do they look ugly and make a tangled rats nest of wires” We use them on our plant and have some additional accessories for them like mounting carriers (also DIN Rail mounted) or gel boxes (gel filled box suitable for splicing terminal for instant IPX8 rating).
Same here. I used them on a Radio station build a couple of years back for some relay logic wiring we needed to do. Those busses and DIN rail holders are great. The install looks good and since I used wiring color codes to keep the hundreds of wires manageable, it is easy to see where a wire is meant to go should it come loose. Not that I expect it will.
The smart-alec-y answer to the title question is: learn to solder. :-)
The dumb answer to the title question is: I have “fixed” many things by just twisting wires together and taping them.
I’ve used some of the knockoff Wago. (in low voltage applications only due to certain concerns). I want to like them, but the bulk just makes it harder to navigate the equipment enclosures where I’ve made adaptations. I do like the point about joining stranded to solid wire with them. I expect to find a home for them in prototyping/development efforts.
The even more smart-alec-y answer is to link to the comic :)
https://mightyohm.com/files/soldercomic/FullSolderComic_EN.pdf
The counter-reply to both of the “smart” replies is: this doesn’t help at all if your hands shake enough that applying the iron is more likely than not to shift the parts away from where they’re supposed to be.
Soldering is time consuming, makes fumes that are nasty in tight spaces, requires reinforcement to not make stranded wire brittle and delicate, and is hard to undo. I’d go for twist and tape in quite a few cases if I didn’t have a wago.
I have the solder-seal kit and have used it.
It takes a tiny bit of fiddling/learning to get it right, but it forms a strong inline match between wires.
Typically the seal is much more flexible than the insulated wires going in, so that the sealed wire bends at the seal making the seal seem floppy and flimsy. You can compensate for this by sealing several wires in a bundle and adding a stiffener such as the cut-off end of a cable tie, inside a bundle-sized shrink-wrap tube.
It looks more professional than soldering twisted ends and wrapping with electrical tape.
Other than the professional look, I really don’t see the utility of using the solder seals. It’s an extra box of stuff you need to carry around (plus a heat gun), and the floppy-ness of the seal requires extra work to stiffen up.
I absolutely *hate* crimps, because you can never tell when the crimp failed. Crimp a connector and then always tug on them to make sure it’s a sound connection… half the time they fall apart in your hand, and it’s better to notice this early.
I know this is a generic problem with crimps because I’ve had crimps from purchased devices come apart on me. Lots of times I’m left holding a stripped wire in one hand looking at the crimp connector still connected to the tongue on the device. Without having tugged on the wire.
For that reason I always solder the wire to a crimp connector. It’s a complete PITA, but when working on client’s hardware it’s usually time well spent.
(Also: I always go over the client’s hardware with a hot glue gun, giving a strain relief to every wire directly soldered to a PCB or control. Many, many problems can be avoided this way.)
Well, I have to say, the crimper matters, as do the crimps themselves. The ones that cost a fortune work just about every time. They have to be sized for the wire properly too. Neatness counts, as does strip length.
The ones from Amazon will fail all too often and exactly as you describe. It’s not worth the potential havoc.
I think you are using the wrong kind of crimps or the wrong* Crimp tool. I learned Honda “warranty repair” crimps in college. You are crimping to bare metal with the proper tool, and it ratchets down, it will not release until you achieve a proper crimp. A proper crimp is worth it for a few reasons: it is gas tight (it actually stretches the metal into something resembling an organic fiber). It is vibration resistant because it exits at a curve instead of a hard point, a ‘stress riser’. It can be done easily and repeatedly without extra power or fuel.
If it is good enough for Honda I am not going to complain about it.
* I will make a crimp with the in appropriate tool, on those cheap plastic covered ring/spade/splice terminals I will always use the tool with the little bump on the side for unshielded terminals. I want it to be a proper solid joint.
Also a USB PD solder iron (like T12 etc) can be had for $18 shipped if you shop around, or a basic AC pencil for much less. (Heck even a 20v laptop PSU or drill pack power breakout and a bare “24v” iron will work pretty well and cost about $10 if you needed portable)
Soldering iron that runs off lighter fluid.
…or butane powercells. or from a 12v cigarette lighter socket. (I have at least 6 soldering irons, including the aforementioned)
“I absolutely *hate* crimps, because you can never tell when the crimp failed. Crimp a connector and then always tug on them to make sure it’s a sound connection… half the time they fall apart in your hand, and it’s better to notice this early.”
If you have crimp connections that fall apart then the crimp tool was worn out, not set up correctly or were using poor quality or the wrong sized connectors for the wire.
Even the cheap crimp tools can make good crimps if you know how to set them up and use them with the correct crimps, wires etc.
Crimps are only good if you paid big money in my experience.
I have used the solder sleeves before but they give me bad vibes. The 3M ones I used last never really seemed to flow into the wire just kind of melting around it looking like a cold joint. I mean it worked but its not something I would trust on, lets say, a car
Or an airplane. I don’t think there’s a decent flux in those things, and let’s talk about low melting solder along with that possible cold joint you also noticed, heating and oxidizing of the conductor inhibiting wetting, and you’ve got a recipe for gremlins.
Ejection seats have quite a few of them in the wrong harnesses. Done properly, they work really well
I’d not trust a soldered wire joint on a car for anything other than the most temproary of bodges (they do have a bit of a habit of becoming permanent though) because you really have to be careful to support it correctly against vibration or it will break.
Lead free solder in the 3M ones perhaps?
I had a broken wire in an injector harness in an earlier car. It was intermittent, it would be fine for days then suddenly it was firing on just 3 cylinders for a while, happening more frequently and for longer as time went by. It went to the dealership 3 times without a successful diagnosis, before finally I set the engine idling and started prodding around the engine bay until I found the cause. The wire that was broken was within a multi-wire harness that itself was sitting in a plastic channel for support. I can only guess that the wire was mishandled during harness assembly, or during a prior service. I can’t remember any service that would have removed that harness from its support though.
Ten minutes later I had that sucker soldered and taped up, and it never gave me any trouble again in the next 150000+ miles before the car got totaled.
I think vibration is generally overrated as a destroyer of solder joints. The problem (when it occurs) is usually the wire failing where it meets the joint, and not the solder joint itself. Vibration in the wire causes repetitive stress where it meets the stiffer connection. That leads to work-hardening of the wire and an eventual break. Here’s the thing though – the same thing will happen at any stiff connection point in the wire if it is not mitigated. Solder, crimp, screw terminal, etc.; they are all at risk. That’s why connectors intended for wires subject to movement (e.g. guitar leads, headphones etc.) have strain relief where the wire meets the connector. Provide strain relief for your solder joints (or crimp or screw terminals), and you’ll prevent the problem. Heatshrink or electrical tape is usually sufficient. Make it so that the joint and wire can only move together and it’ll be fine. If your fix is relatively bulky compared to the wire, give it some additional support. Tape or tie-wrap it to other parallel wires, or to something solid.
It’s not rocket science (unless of course, you’re working on rocketry!)
Soldering should not be a barrier to entry into the electronics world. But alas, solderless breadboards leave a lot to be desired. Now that Pololu, Adafruit, and Sparkfun sell “carrier boards” that make prototyping with surface-mount devices so much easier, gee, why hasn’t wire-wrapping made a comeback? …or some other way to build prototypes that don’t fall apart… Me, I dream of little solder rings you can crimp onto thru-hole pins and melt with a hot-air solder station.
It took me years to learn how to solder well. It is exacting work, sensitive to the melt-point of solder, crud on the soldering iron tip, and 1,000 invisible details (I use a microscope now). Holding wires together so I can solder with only two hands is always my biggest challenge. It requires patience. (Maybe someone will write “Zen and the Art of Soldering.”)
0.1″ headers on a carrier board, and female jumpers, is a very nice way to prototype.
I do enjoy wire-wrapping on occasion
I love the Wago connectors. Just be sure you’ve got a tight grip, and can’t easily pull the wire out. If it’s in there, they usually stay pretty well. I’ve used them in outdoor and vibrating situations and they hold very well.
I recall using raychem solder-seal type connector way earlier thyan 1988. Use used then to prapir certain types of aircraft wiring faults, especially in F-4E aircraft since the ECM was all “add on” from the earlier designs. We also have a version that was call a “video splice” that had prewired leads and was designed to terminate to a coax. We had a hot-air gun that looked like a desoldering pencil except with a reverse airflow.
I recall replacing one in Korea during a Team Spirit excercise in 1985. On the right wing of an F-4 in February. It was cold…. damn cold. At least a Tab-Vee would have cut down on the wind.
So the 1988 patent had to be for an improved version of some sort.
That 1988 patent has citations to earlier (first from ~1960) connectors using same method, but slightly different form factors?
Can’t believe nobody mentioned ‘chocolate block’ yet…
Hydraulic crimper and lugs! You can pull a car out of a ditch with one of those connections!
Yes, I just got a 10-ton crimper for $26 on Amazon. Deal.
I don’t like the low melt solder things, I think a crimp splice and seperate piece of weather seal shrink is the way to go.
Amazon crimpers mmm, you will like Louis Rossmann latest video “The Downfall of Amazon: Dangerous Products, Fake Reviews & Vanishing Brands”, he shares his experience with Amazon crimps :)
Thank you for your valuable comment! Amazon is full of scam products. I’d like to add that it’s important to read both the positive and negative reviews of a product and pretty much ignore the actual rating. Many genuine reviews of happy owners are actually from people who haven’t used the product for a long time or don’t know how to rate the quality of the product. The same applies to some of the negative reviews. I’ve seen products with good reviews and the one negative review informs me that the product simply doesn’t work for what I intent to use it for.
Amazon makes it worse in mixing reviews. That’s why it’s good when reviewing to provide identifying information so people will know exactly what you bought.
for non-solder you can’t beat wire wrap https://en.wikipedia.org/wiki/Wire_wrap I used to use it a lot, and it’s removable, great for prototyping.
In the 1980s I worked at a science museum where I designed & constructed all of the electronics for the exhibits. I used wire wrap—*massive* quantities of it—exclusively, because at the time it was too expensive (for us, anyway) to get PCBs made. Debugging was an absolute nightmare.
I went through a lot of those flimsy little battery-operated wire wrap tools, and sometimes just preferred to use a manual one because (in my hands, at least) the results were much better. You had to hold the power tool just right to get a neat wrap, but with the slower manual one it’s pretty hard to screw up.
My father taught me how to weld when I was 10 years old. I still have problems sometimes, but in this case I blame the hardware.
I sometimes had experience with PCBs with heavy components whose mechanical attachment to the PCB is the same as the electrical connection. In this case, an invisible micro-crack frequently occurs, particularly on wave-soldered PCBs with little soldering. This often leads to temporary failures due to hot expansion phenomena which make troubleshooting complicated.
I have worked in a number of environments and I use pretty much everything depending on the application. Vehicles, I either use solder-seal or standard soldering with heatshrink or very high quality electrical tape, it depends on the current and circuit.
The NASA standards are really good for anyone joining wires though. Highly recommend.
For things on the can bus, I never want to cut the existing bus so it is always stripping and soldering a wire on and then taping with super 88 or 3M 37 tape as it seals over itself quite nice when the conductors are warm and doesn’t leave goo in a year. Add a ziptie a couple inches back as a strain relief. For large current wires, I solder and tape or heat shrink. Most of my automotive stuff was large wires and you usually try to avoid cutting manufacturer cabling regardless, so it was soldered with a torch or gun, taped over and ziptied to keep it secured. For any new cabling, power cables were spliced and soldered with a thick adhesive-lined heatshrink over it to make it water resistant and durable.
Crimp connectors were always for ground and power connections and I prefer a proper ratcheting crimper with a heatshrink boot to seal the wire on both sides of the crimp and try to prevent corrosion.
For anything I build, I like sturdy connectors to manage the wires. The solder in terminals are great for 12v stuff as I already have the tools for proper crimping etc. https://ca.rs-online.com/product/rs-pro/534834/70639646/ https://www.aliexpress.com/i/33042700813.html
And there is nothing inherently wrong with the “idea” of scotchlok connectors… but so often the issue is poor installation by people with no experience in areas they shouldn’t be used. I have had to replace and redo so much wiring that was destroyed by these things I just outright avoid using them myself and mutter expletives whenever I come across them. :/
The said NASA standard: https://nepp.nasa.gov/files/27631/NSTD87394A.pdf#page=71
And an excellent NASA instructional video from 1958 to go along with it! https://youtu.be/_RXugDd0xik?si=Tw7kDs9lKscv5uMm
The secret of the Wago connectors is their ingenious connector (Wago call it the “cage clamp”). It’s a spring-loaded connector that is (at least for series 222 and 221) opened with a lever, but closing the lever doesn’t clamp the wire—the spring-loaded connector does. There are series of Wago connectors that don’t even need a lever, as you can directly push in solid-core wire, which will then be clamped by this connector. The nice thing is that the correct clamping force is inherent in the design of the Wago connector and not dependent on the user (as is the case with screw terminals, for example). That said, they’re not perfect, but they do come pretty close if you have the space. Wago connectors aren’t cheap, but in my opinion, they’re worth it nonetheless: clamped wires can be reused and rewired pretty much indefinitely, as opposed to any other connector that severely damages the wire when the connection is opened. You also don’t need any remotely special tools whatsoever (e.g. heat guns, very expensive crimping pliers, etc.) and they fit a wide variety of wire sizes, so you don’t need to bring lots of different components either. Yes, they are quite costly, but given the convenience and ease of use, I reckon you’d be hard-pressed to justify using anything else if there wasn’t some very compelling reason to do so.
I mostly use solder joins myself, but do whip out small wire nuts while testing low voltage dc power stuff
Was wondering if anyone would mention these. They are IMHO the worst way to connect wires. Twist or don’t twist the wires together? Twist right or left? Strip just the right length. And when you finally get the nut in place, one wire falls out or gets pulled out with a light tug.
If I haven’t already mentioned it…I hate wire nuts.
I literally threw away my large collection of wire nuts after I discovered glorious Wago connectors some years back. I thought I might regret that when I found a situation where the bulky Wago thingy wouldn’t fit, but so far it hasn’t been a problem. Now, wire nuts seem unbearably primitive.
From getting certified for marine electrical work, I learned how to do proper crimps. In a nutshell: standardize on a good brand of crimp lugs, then get a good controlled-cycle (aka ratcheting) crimper and adjust it to work with the chosen lugs. Cheap crimp lugs (Harbor Fright or far-east) are often unreliable, especially in the larger sizes.
Marine and other standards do not like simple soldered connections; if the joint overheats, it separates and then you have bigger problems. These standards call for crimped connections. You can solder a crimped lug afterwards, but for a proper crimp it’s superfluous. For these reasons, I wouldn’t touch those solder-seal things except for a low-current signal connection, and they’re too darn expensive anyway.
Finally, simple wire-to-wire crimp connections suggest a lack of planning. i would rather use a terminal strip of some kind when a number of related connections are required.
Bonus topic: who crimps on ferrules for wire to eurostrip terminations?
“standardize on a good brand of crimp lugs, then get a good controlled-cycle (aka ratcheting) crimper and adjust it to work with the chosen lugs.” Never had a problem with regular non controlled crimpers but heard many times that other had – there ware at least 2 good articles about crimping on HAD and commenters mentioned that – so I don’t test my luck anymore.
“You can solder a crimped lug afterwards, but for a proper crimp it’s superfluous” I am not an expert but to my knowledge you should not do that. Soldered strands become more prone to damage when bended. In mentioned HAD article about crimping some commenters mentioned that.
You can solder a crimp but you really shouldn’t need to and probably shouldn’t because it takes away one of the major advantages of stranded wire, flexibility, and creates a stress point (probably the wrong terminology but I can’t think of better at the moment) as well as wicking flux up into and under the insulation, some types of flux can become corrosive when they absorb moisture.
That was my point when when I wrote: ” Soldered strands become more prone to damage when bended” But I also temporary run out of proper terminology.
“Bonus topic: who crimps on ferrules for wire to eurostrip terminations?” Europeans!
(Being funny, but also not.) It’s quite common here in Germany for screw-terminal applications like hooking up lamps, etc. I’ve taken to doing it, and it’s pretty clean.
Beats wire nuts, although that’s what I grew up with, and have a certain nostalgia for.
The solder seal things have never failed me, but I greatly prefer Wago. I use them for basically everything.
I know Wago connectors are allowed on building power wiring in the USA but are crimped connectors and solder-seal connectors?
Solder seal: I think most inspectors would nix them, but maybe with a proper lineman splice technically yes, if you can find any that are properly listed and use the proper installation procedure. NEC 110.14 states “Soldered splices shall first be spliced or joined so as to be mechanically and electrically secure without solder and then be soldered”.
Crimp: If properly listed crimps are used, fine. They are quite common in some circumstances, and sometimes preferred, such as with large gauge cable, or when wiring machinery using SO cable.
I use wago’s for my home made kite’s. They hold the bamboo and the carbon fiber rod’s very well.
Though I’ve have used a few alternatives I grab my gun first. Most times something doesn’t solder right quickly it’s dirty and needs flux. Invest in a little can of flux, sometimes it’s all that’s needed on some rework. Weathered auto wiring always needs some on repairs, the flux in even good solder isn’t enough.
Beanies (a.k.a. Dolphin connectors). Particularly the gel-filled ones. Scotch-Lok connectors. Both of these types are for small-signal applications such as telecom and alarm wiring.
Ah, I have a couple when I use to have a land-line. Just waiting for fiber and those connectors.
Beanies, a.k.a. Dolphin connectors. Particularly the blue, gel-filled ones. ScotchLok UR, UY, etc. Both of these for small-signal applications such as telecom or alarm wiring.
Where’s the Lüsterklemme (“luster terminal”) ? 🙁 I can’t believe the article has a ll those weird connections, but not the traditional terminal strip. So weird to me.
I mean, I’ve never seen one of those Dr. Schiwago connectors, for example. Or those blue things.. Anyway, it’s fascinating to learn what’s out there. :D
Indeed, I also use terminal blocks a lot when I want to keep things removable. Never heard them called Lüsterklemme though, but that’s not the point.
Pardon, my bad. 😅 It’s the German term. I’ve added it, too, to make sure what I’m referring too.
Because, I’ve learned the hard way that there are many subtle differences between my language and English language.
It’s not so much about right/wrong, but about cultural differences and daily life.
There’s also some kind of false security that’s sort of a trap. You grew up with English films or novels and think things are alike, but then they turn out to be very different at times.
Words are also different, there are a lot of “false friends”.
A German “oldtimer” is a vintage car rather than an elderly man with life experience (though the real meaning is slowly being understood, too).
Or, the German “smoking” refers to a galasuit. An English man would be (rightfully) confused here.
Or, in German you ask “Verzeihung, haben Sie Feuer” if you ask for a light. In English, asking “excuse me, do you have fire?” would be quite amusing.
Or, “gymnasium”.. In German, it’s a school similar to a college, maybe. In English, it’s a sport’s hall for exercising.
An “exercise” is often associated with an exam among German students, rather than sport activity. They’re also “making sports” (Sport machen) in German rather than doing an exercise.
“Driving a bicycle” is also a possibility here, rather than riding it. :D
So yeah, lot’s of material for a little confusion. 😅
Sorry for the long comment of mine, too.
I’m in the EU and do in fact understand German. I just watched a bunch of German YT’s actually. And I also made the driving v riding mistake. I even argued that technically since you power a bicycle you are ‘driving’ it and since you are not powering a car you are ‘riding’ it :)
Anyway, that why I was surprised I did not hear the term you used. Not that my German is THAT great though that I would know such regional technical terms
Your post with the various language traps is still interesting for the other readers of course.
I searched the internet for pictures of ‘terminal block’, then immediately thought “ah, Lüsterklemmen” … for me it is mostly missing vocabulary that leads to “write now, trans later”, which then never gets done :-/
speaking of vocabulary … s/’terminal block’/’eurostrip termination’
What happened to the old twist and tape? 😬
I was just going to mention this. I bet there isn’t a single self-taught person here that didn’t connect two wires the wrong way first when they were kids 😁
Good point. I did the twisting thing, too. It worked best with cables; wires often broke. Also used electrical tape.
A few years ago I learned that the US electricians from overseas have these plastic caps for that purpose. They can be screwed around the wire connection.
They’re made by “WAYCO” it seems. Pictures: https://de.aliexpress.com/item/1005005211242430.html
In my place, though, we rather used terminal blocks and shrink wrap.
Entering the realm of electronics shouldn’t be hindered by the need to solder. Unfortunately, solderless breadboards fall short in many ways. Given that “carrier boards” from companies like Sparkfun, Adafruit, and Pololu make surface-mount device prototyping a cinch, why hasn’t wire-wrapping been more popular? ..Perhaps another method for creating prototypes that are sturdy… I myself have a dream of tiny solder rings that you can melt with a hot-air solder station and crimp into through-hole pins.
Investing a small amount of flux can occasionally suffice for a rework.
All these comments and nobody has mentioned Anderson PowerPoles? These things have become the defacto connector of choice for ham radio as far as I know. Easy enough to install, though the proper crimp tools a bit pricey, genderless, high current capacity.
They’re good, but proprietary. More and more hams are accepting them, too, yes. But I prefer the free (non-parented) banana plugs or common lab plugs (they’re not exactly same). That’s in harmony with ham spirit, too, I think.
Open Source and Open Hardware should be supported more in ham radio, I think. I remember the days when all ham computer projects were completely dependent on MS Windows.
PowerPole is same monopoly, with the exception that Windows had clones (ReactOS) and alternatives (WINE). MS-DOS had compatible OSes, too.
Anyway, I’m not surprised anymore. People are less and less willing to make sacrifices in order to keep their values. It’s just sad that ham radio is also affected since a while. Because, it used to have morals/values. To me that trend is just a bit depressing.
Btw, I didn’t mean to say PowerPole plugs are bad somehow. Rather the opposite, they’re neat. They’re also hermaphrodite, for example .
It’s just.. There are no second sources like there used to be with early processors (m68k, Z80, i8086, i80286) for example.
If the company behind PowerPole would dissolve for whatever reason, they weren’t available anymore.
The lower end banana plugs are independently made, by contrast. There are numerous companies making them, with varying quality.
Also, banana plug replacements can be built at home in a DIY dashing. It’s just a connector with a hole/plug. You can even bend a wire and plug in the connector directly.
In a situation were communicating really is important, the banana connector or UHF is a lifesaver. It can be fixed in a hacky fashion.
That’s also why I stick to simpler connectors. They mean freedom and independence. You still can improvise in a MacGyver style, too.
Just take the N connector. It’s great for several reasons (water proof, exactly 50 ohms), but the plug is tricky to solder. A poor UHF connector (PL259/SO239) is the opposite.
I have been using Posi Lock connectors for some time. They are a little pricey, but made in the US and family owned. They are 100% reusable and have for me at least survived some nasty conditions. https://www.posi-products.com/index.html
Motorsport/Aviation wiring is likely the best ‘universal’ standard of wiring to adhere to. The general methodology is that your wiring should be water, fire, and UV resistant by default, and should be assembled by crimp connections that exceed the strength of the wire(s) they connect. It’s basically the inverse of this article, where soldering is your absolute last choice when you can’t crimp.
This type of wiring utilizes connectors like DT, Weatherpack, Ampseal etc that are commonly available, modular, and water/fire/UV resistant. Connectors are “pinned out” using crimped male and female pins, which can be removed/reinserted to fix an pinout error or modification.
Motorsport commonly uses TXL/GXL wire, which has a wide temperature operating range and is UV and fire resistant. In extreme applications milspec M22759/16 and M22759/32 Tefzel wiring can be used. Permanent wire-to-wire connections are made via crimp splices, open barrel crimps, U splice crimps, etc.
It takes a bit to get set up, a good crimp tool (Hozan P-707 is a good universal crimp tool to start with), splices, and lots of good heatshrink (3:1, dual wall, adhesive lined, fire resistant). There is a bit of a learning curve in crimping effectively, you should always test your crimps using a significant amount of force, the wire should break before the crimp fails. However, I would never go back to soldering by default. It’s fantastic to be able to complete 95% of wiring jobs without having to bring out a 300C iron, especially when most of my jobs don’t fit on a workbench.
I’m a low voltage tech by trade and I use B-Connectors with most of my splices and terminations. They’re the cheapest and come in a variety of colors.
i am 43 and i’m finally pretty alright at soldering, *but* my hands shake like crazy too. so it’s still kind of stressful to me. i’m upset about it.
these sort of gadgets are great but they can’t replace solderig for me. soldered connections are just so much more space efficient (or can be). i just did a project with about 20 solder joints in it and one of them was an overlap splice that required a bit of shrink tube and it was just amazing how much more space even that one joint consumed, compared to all the other (flimsy dead bug or through hole).
my dumb hack to ease my burden a little bit is that when i can, i use wire wrap wire and then i solder over that. that way i don’t need the square-peg sockets, and i get the convenience of a wire that doesn’t bounce around when i shake.
there is a blue dyed “suprglue” from a well known manufacturer, which is conductive. used that long ago to fix my vespas ignition (hv cable). your own mix should do the same trick. greg dont stress yourelf, soldering action is relaxing for me (i can do fine-pitch with a common iron). im 43 aswell atm….
Spent one summer as a teenager in the late 70’s after the Apple ][ was released building clones from scratch. My old man was an electrical engineer by education and hacked together radios for a hobby. We (my two brothers and I) each got 75W guns and learned how to solder ICs to bare PCBs, and more important, we learned how to unsolder anything cleanly using good old unsoldering wick (and generous squirts of isopropyl alcohol). We learned how to recognize a cold solder joint and how to spot bad traces and shorts from crappy boards. Probably suffered brain damage from inhaling the fumes of lead-based solder and caught quite a few pieces of hot flux in the face and many singed finger tips. Still my go-to way.
For low volt, small gauge wire you cannot beat Scotchlok splices. They come in various forms to do 1 to 1 splices, 3 way splices, and taps. They are filled with dielectric gel so they will even hold up in out door applications. They do not require stripping the wire either. You just insert it and squeeze the cap with pliers (or a special tool that has the exact right spacing). They are cheap and reliable. Pretty much any wire that will fit int he insertion holes will splice just fine. Old telecom heads use to use them all over when copper telco was at it’s peak and I learned about them working IT for a hotel as the old telecom engineer there used them for the PBX wiring. I HIGHLY suggest them to those who may not be aware. You can get them on amazon or any hardware store.
Amazon also sells locking pressure crimps that are similar to scotchlok splices, but handles slightly bigger gauges of wire. They do not have the dielectric gel. I have found them less reliable than scotchlok splices, but they can still be handy as you can use 18 gauge wire and they can do mains voltage (for low amp loads).
The Russians crimp everything on their airplanes? That must be a significant penalty on fuel and weapons carrying. We should do EVERYTHING we can to encourage the continuation of their “crimp-only” policy. 😳
Please be kind and respectful to help make the comments section excellent. (Comment Policy)
This site uses Akismet to reduce spam. Learn how your comment data is processed.

Custom Litz Wire For Motor Winding By using our website and services, you expressly agree to the placement of our performance, functionality and advertising cookies. Learn more