KraussMaffei and its partners are exhibiting the PX 321-1400 at Fakuma 2023.
For MuCell, KraussMaffei has created the new HPS-Physical Foaming screw with a longer three-zone area, which can be universally used for all plastics (with and without fibre reinforcement) and has a plasticizing capacity that has increased by up to 30 percent. The company claims that this allows for the selection of lesser screw diameters than before, which significantly reduces investment and operating costs for the plasticizing unit, or for the generation of a greater output using a screw of the same size as before. Injection Molding Labeling

Due to the development work, KraussMaffei commands wide-ranging expertise with regard to all MuCell screw designs currently on the market and has been able to test variants of the front and centre check valves and single-flight and double-flight three-zone areas using a modular system.
The APCplus machine function has also evolved and is now being used with a gas-charged melt for the first time. APCplus shifts the changeover point and the holding pressure profile from shot to shot based on the measured melt viscosity, which results in extremely weight-constant components.
The trade show application, a storage table for trucks and commercial vehicles, features a few more technical highlights demonstrating that physical foaming is of interest even in areas that may have seemed off the radar until now. An entire team of project partners worked toward this goal. The story begins with the surface decoration by in-mould labelling, for which Isosport (Eisenstadt, Austria) supplied a suitable film preventing the formation of bubbles by the outgassing nitrogen.
For the mould, Wirth Werkzeugbau (Helmbrechts, Germany) put all its skill to use—for instance for the opening stroke, which lets users achieve the maximum possible degrees of foaming. Usually, immersion edges are required for this process, but Wirth managed without them thanks to its expertise. For moulds for MuCell, precise cooling is particularly important to prevent what is known as the post-blow effect. This effect makes bubbles emerge on the surfaces after the process—while the melt in the interior of the component is still hot—and renders the part unusable. In the trade show application, special mould cooling channels ensure uniform cooling at the surface—without variothermal technology—and safely prevent hot spots.
Immaculate exposed faces without streaks
In addition to the cooling, the graining by Reichle (Bissingen/Teck, Germany) makes a crucial contribution to achieving perfect exposed faces on the foamed components. Another prerequisite for the streak-free surface aesthetics is a suitable material. Partner Lyondellbasel has a wealth of experience with polyolefins in the visible area of foamed components and already supplies them to OEMs.
In addition to the cooling in the mould, an efficient machine-side temperature control system is necessary. The system Orca is provided Jurke Engineering. Orca measures the speed and quantity of the flow by ultrasonic means—from the outside and without contact with the medium. The precise temperature control optimizes the cycle time.
As usual, Trexel is a reliable partner with whom KraussMaffei has been successfully collaborating since 2001. The metering system originates from this partner. It is fully integrated into the KM MC6 control system and consequently ensures very easy, intuitive handling. If necessary, even satellite solutions are offered that allow multiple machines, all fully integrated, to be supplied with the necessary gas using only one compressor.
An LRX 150 linear robot from KraussMaffei picks up the blank film from a drawer in which four different film types can be kept close at hand. Then the robot puts down the selected film on the cleaning station, where all particles and/or contaminants are removed using a cleaning brush from Wandres (Stegen, Germany) and the matching extractor system from ESTA (Senden, Germany), two more of our partners. The robot gripper executes a turn concurrently with the cleaning process so that clean suction devices pick up the cleaned film again.
Then the "stack gripper" inserts the film into the mould, and the finished part is demoulded. Demolding is followed by the handshake transfer to a second robot for a foam structure test of the component by means of a testing system from Teratonics (Orsay, France). The testing system specifically allows users to visualize the compact outer layers and the spatial distribution of the MuCell foam in the interior of the component and to assess the production as free of bubbles. After this test has been completed, the component is placed on a conveyor belt and transported out of the automated system.
All data at a glance
The easyTrace 2.0 systems collects all data related to the injection process and the structural test shot by shot and displays it on a screen. In addition, a QR code appears under which all process parameters for this individualized component have been stored. Here, easyTrace 2.0 acts as an interface system that gathers all data of all process nodes and functions as an interpreter for existing customer-side MES or ERP systems.
MuCell provides a wide variety of options to reduce the CO2 footprint through material and energy savings. The trade show application demonstrates that it succeeds in doing so even in the production of challenging visible parts.
European Plastic Product Manufacturer
Part of Rapid News Group
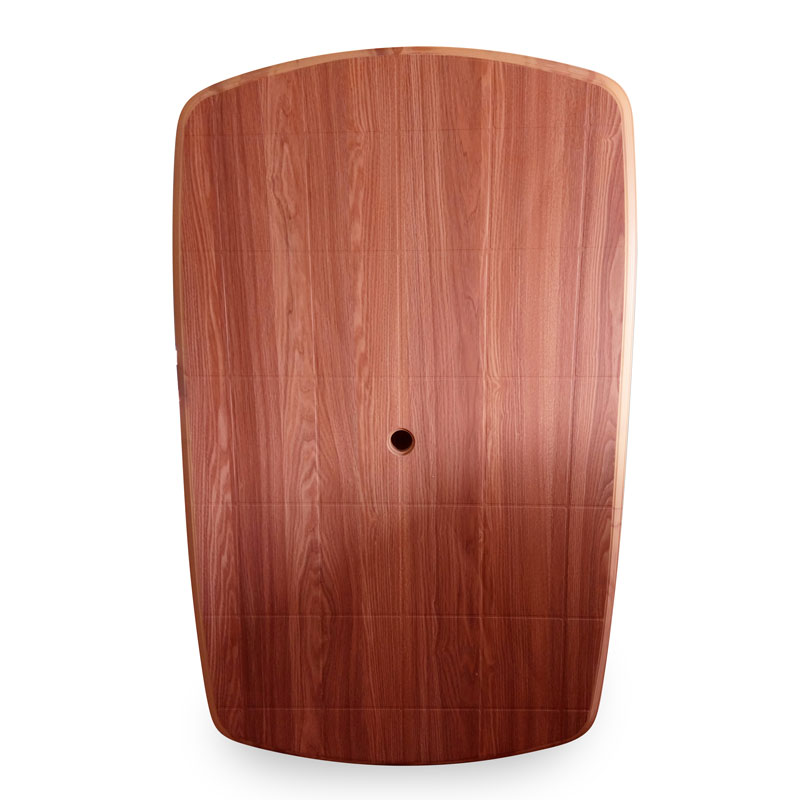
Iml Products © Rapid Plastics Media Ltd. A Rapid News Group Company. All Rights Reserved